Top Tips on Waterproofing for Flat Roof Durability
Waterproofing for flat roofs is vital for preventing leaks and water damage. Flat roofs are more susceptible to water pooling, which can lead to serious issues if not addressed. This article covers the best methods for waterproofing for flat roofs, how to spot damage, and maintenance tips to keep your flat roof in top condition. Proper waterproofing for flat roofs ensures longevity and durability, effectively protecting your investment.
Key Takeaways
-
Waterproofing is essential for flat roofs to prevent water pooling and UV damage, ensuring longevity and structural integrity.
-
Regular inspections for cracks, blisters, and water pooling are crucial for early detection and repair, minimizing potential damage.
-
Choosing the right waterproofing method and sealants, such as liquid rubber or elastomeric, enhances flat roof durability and performance.
Understanding Flat Roof Waterproofing
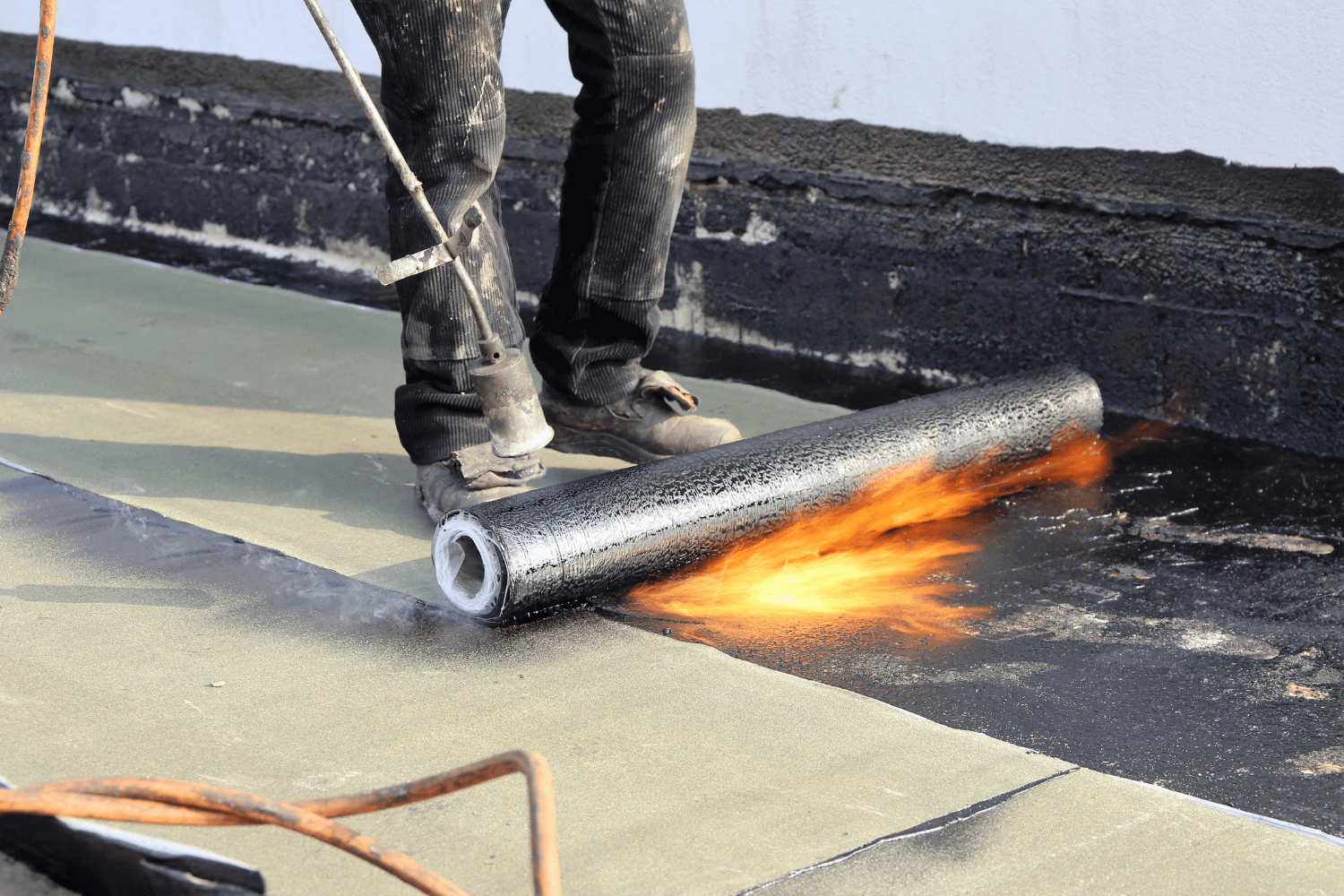
An overview of flat roof waterproofing techniques.
Waterproofing flat roofs is crucial as it shields the structure from water damage and prolongs the roof’s lifespan. Flat roofs, unlike their sloped counterparts, do not naturally drain water, which means they are more susceptible to water pooling and subsequent leaks. This makes waterproofing an absolute necessity to prevent deterioration and maintain the integrity of the building.
Flat roofs commonly face issues such as water pooling and UV damage. Water pooling can lead to leaks, while prolonged sun exposure can cause the roofing materials to break down, leading to cracks and holes. These issues can compromise the watertight seal of the roof, allowing moisture to seep in and cause further damage. Therefore, regular maintenance and effective waterproofing are essential to avoid costly repairs and roof replacement.
Different waterproofing methods, such as liquid waterproofing and reinforced bitumen membranes, offer various benefits tailored to the unique needs of flat roofing. Selecting the appropriate waterproof material and method not only ensures protection against water damage but also enhances the durability and performance of low slope roofs. With proper waterproofing, your flat roof can withstand the elements, keeping your residential or commercial property safe and dry.
Inspecting Your Flat Roof for Damage
Before diving into waterproofing, it’s crucial to inspect your flat roof for any signs of damage. Ensuring safety during the inspection is paramount; use secured ladders and check for anti-skid coatings to prevent accidents. A thorough inspection should focus on areas prone to damage, such as roofing membranes and gutters, as well as any visible signs of wear and tear.
Look for common damage signs such as blisters, cracks, and pooling water. Upon discovering leaks, promptly patching or repairing the damaged sections can avert extensive water damage. Keeping gutters clear of dirt and debris ensures effective water management on flat roofs.
Identifying Cracks and Holes
Spotting cracks and holes in flat roofs is vital, as unaddressed damage can become significant. Alligatoring, a common type of cracking caused by sun exposure and moisture, creates a pattern resembling alligator skin. Regularly inspecting the whole surface of your flat roof can help you spot these cracks early.
Repair cracks wider than 10mm using a flexible mesh with products like Acrypol Plus. Acrypol Plus is equally effective for fixing cracks up to 10mm, providing a durable and flexible solution.
Promptly addressing these issues can prevent further damage and extend the life of your flat roof.
Recognizing Blisters
Blisters occur as air bubbles or pockets of moisture trapped under the roofing membrane. Blisters form when air or moisture is trapped beneath the membrane, posing potential damage. The expansion of these blisters is primarily caused by temperature changes that heat the trapped air inside, causing them to grow.
If blisters are intact, it’s best to leave them alone to avoid further damage. However, if blisters burst, they need to be patched quickly to prevent water from infiltrating the roof and causing more severe issues.
Regular inspections can help you monitor these blisters and decide the best course of action.
Spotting Pools of Water
Ponding or standing water can significantly damage a flat roof’s protective membrane, indicating drainage issues. If water pools on a flat roof for more than 48 hours, it indicates a drainage problem that should be addressed promptly. Immediate attention to ponding water is vital to prevent structural damage from prolonged wet conditions.
Standing water can damage the protective membrane of the roof, leading to leaks and other issues. Regularly inspecting your flat roof, especially after heavy rain, can help you spot and resolve water pooling issues before they cause extensive damage.
Ensuring proper drainage and maintaining the roof’s surface can prevent these problems and extend the roof’s lifespan.
Essential Maintenance Tips for Flat Roofs
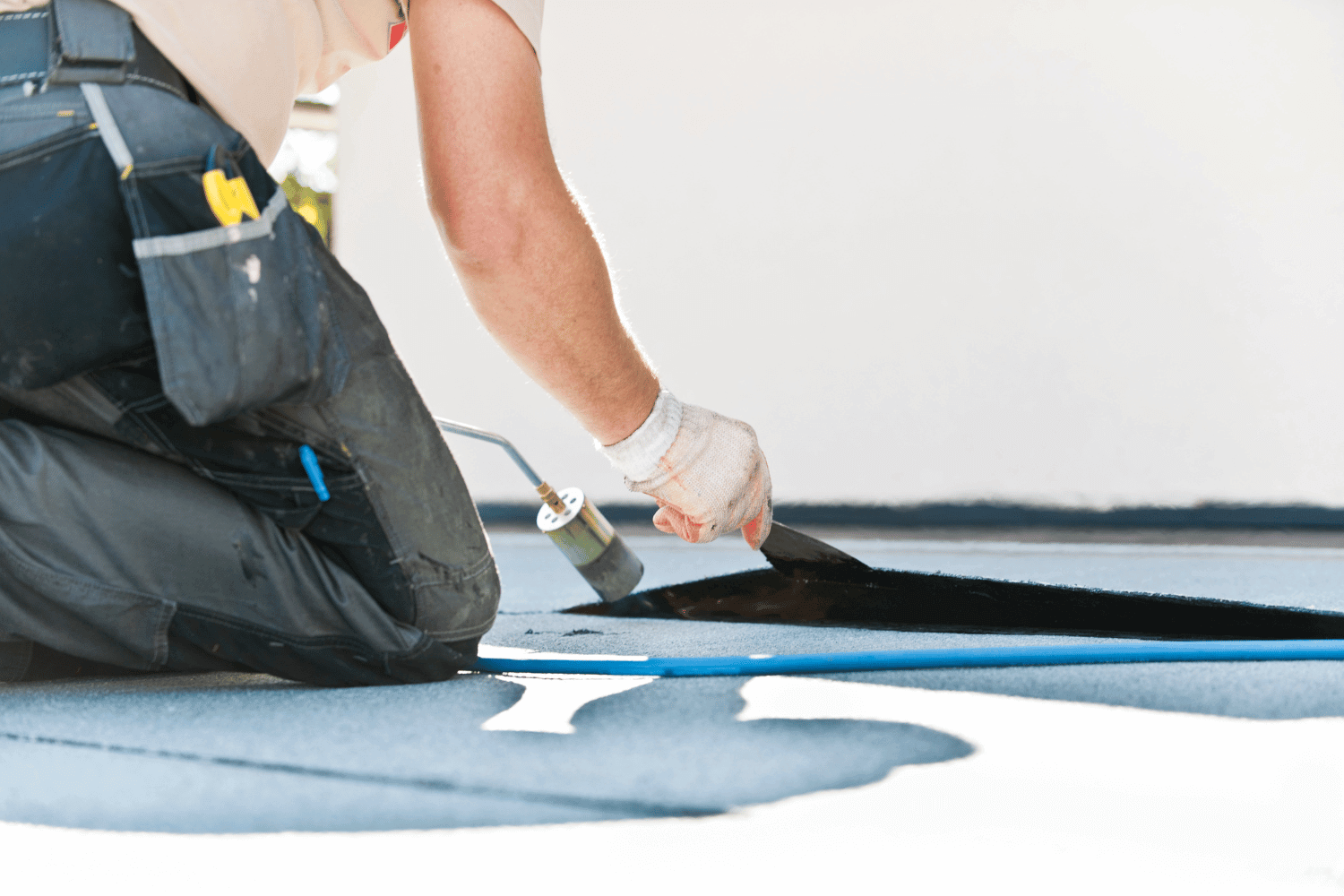
Essential maintenance tips for flat roofs.
Conducting visual inspections of flat roofs at least twice a year, ideally in spring and fall, is recommended. Focus routine inspections on identifying cracks and holes, critical points for potential leaks. Implement safety measures like secured ladders and anti-skid coatings to prevent accidents during inspections.
Removing debris from the roof is another crucial maintenance task. Regular debris removal prevents drainage issues that could cause water accumulation and leaks. Trimming trees and vegetation can prevent surface damage and reduce debris buildup.
Proper drainage maintenance on flat roofs is vital. Keeping gutters clean and ensuring the correct gradient can prevent ponding. In winter, removing snow and ice can reduce weight and prevent collapse. Preparing a maintenance plan for extreme weather events and budgeting for regular maintenance and repairs can help you avoid costly future issues.
Choosing the Right Waterproofing Method
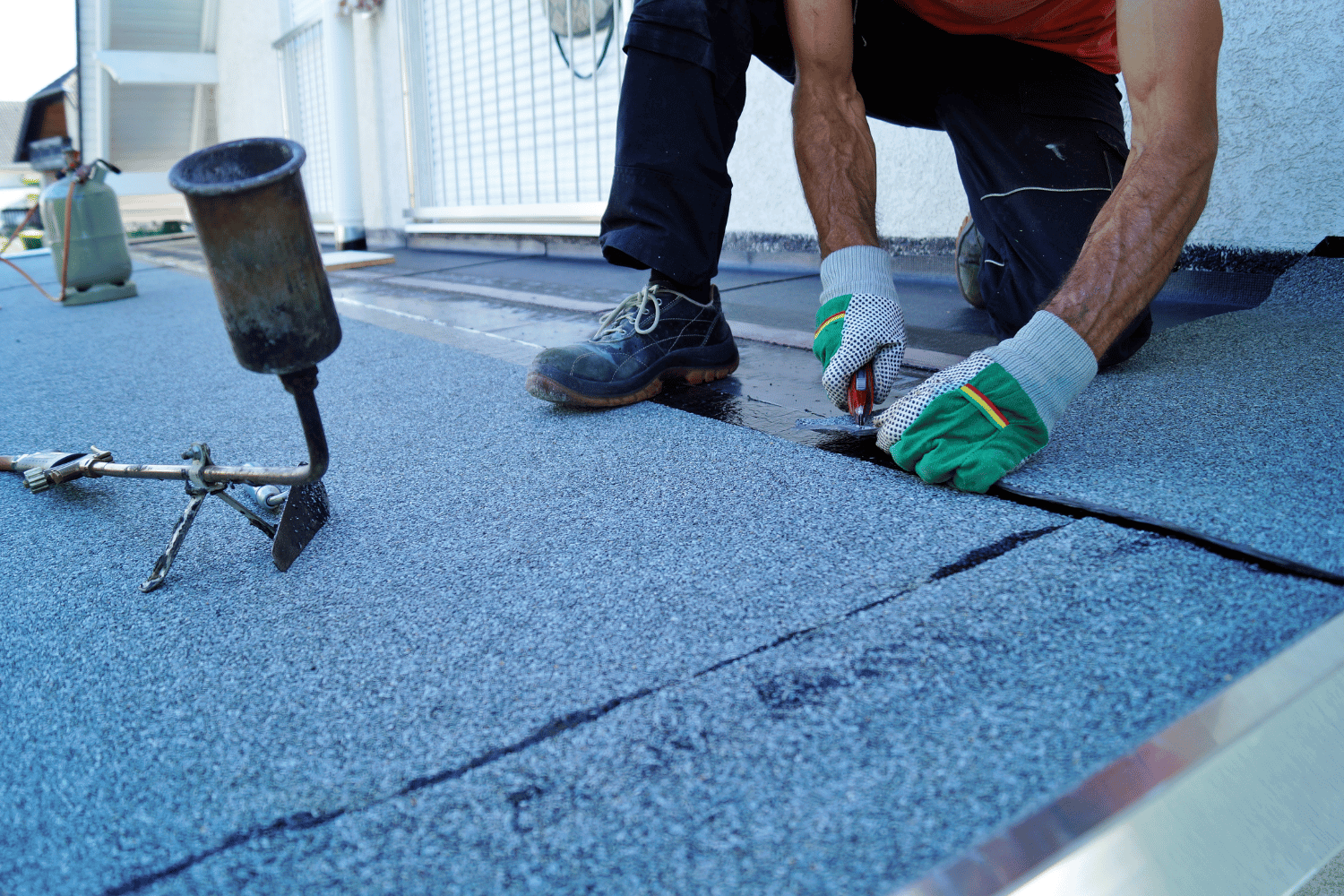
Choosing the right waterproofing method for flat roofs.
Choosing the correct waterproofing method protects flat roofs from water damage. Main waterproofing methods for flat roofs include liquid waterproofing, reinforced bitumen membranes, and single-ply membranes. Each method offers unique benefits suited to specific flat roof requirements and environmental conditions.
Liquid waterproofing solutions, reinforced bitumen membranes, and single-ply membranes all provide effective protection. Factors such as the roof’s specific needs and the environmental conditions should be considered when selecting a waterproof material. A watertight seal prevents leaks, extends the roof’s lifespan, and reduces costly repairs.
Liquid Waterproofing Solutions
Acrylic coatings, a type of liquid waterproofing, are praised for strong UV resistance and adaptability. These coatings create a tough elastic overlay that stops moisture and allows trapped moisture to evaporate, making them ideal for flat roofs. Liquid waterproofing membranes bond directly to the substrate without seams, preventing lateral water migration and offering robust water infiltration protection.
These membranes can adhere to various substrates, including concrete, bituminous membranes, PVC, TPO, and EPDM. Their flexibility, durability, and ease of application make liquid waterproofing solutions practical and effective for protecting flat roofs in various weather scenarios.
Reinforced Bitumen Membranes (RBM)
Reinforced Bitumen Membranes (RBM) are tailored for flat roofing, offering superior waterproofing and durability. RBMs typically employ 2-3 layers for optimal waterproofing, installed using methods like hot, cold adhesive, and torching techniques. This multi-layer application and robust materials contribute to their excellent waterproofing capabilities.
RBM installation can involve materials like hot bitumen, cold adhesive, and self-adhesive methods. These methods ensure a strong bond, making RBMs reliable for both residential and commercial flat roofs. Superior puncture and UV resistance make them ideal for long-lasting protection.
Single Ply Membranes
Single ply membranes like TPO and PVC roofing offer benefits including energy efficiency, durability, and a 25-30 year lifespan. Installation techniques for single ply membranes include ballasting, adhesion, and fastening, with heat-welding used to secure seams. These methods ensure a strong bond, offering reliable protection against water infiltration.
Single ply membranes are mainly synthetic rubber, with EPDM representing ethylene propylene diene monomer. Known for flexibility and UV resistance, these single ply membrane membranes are a practical, long-lasting waterproofing solution. Ease of installation and maintenance further enhance their appeal for residential and commercial applications.
Top-Rated Flat Roof Sealants
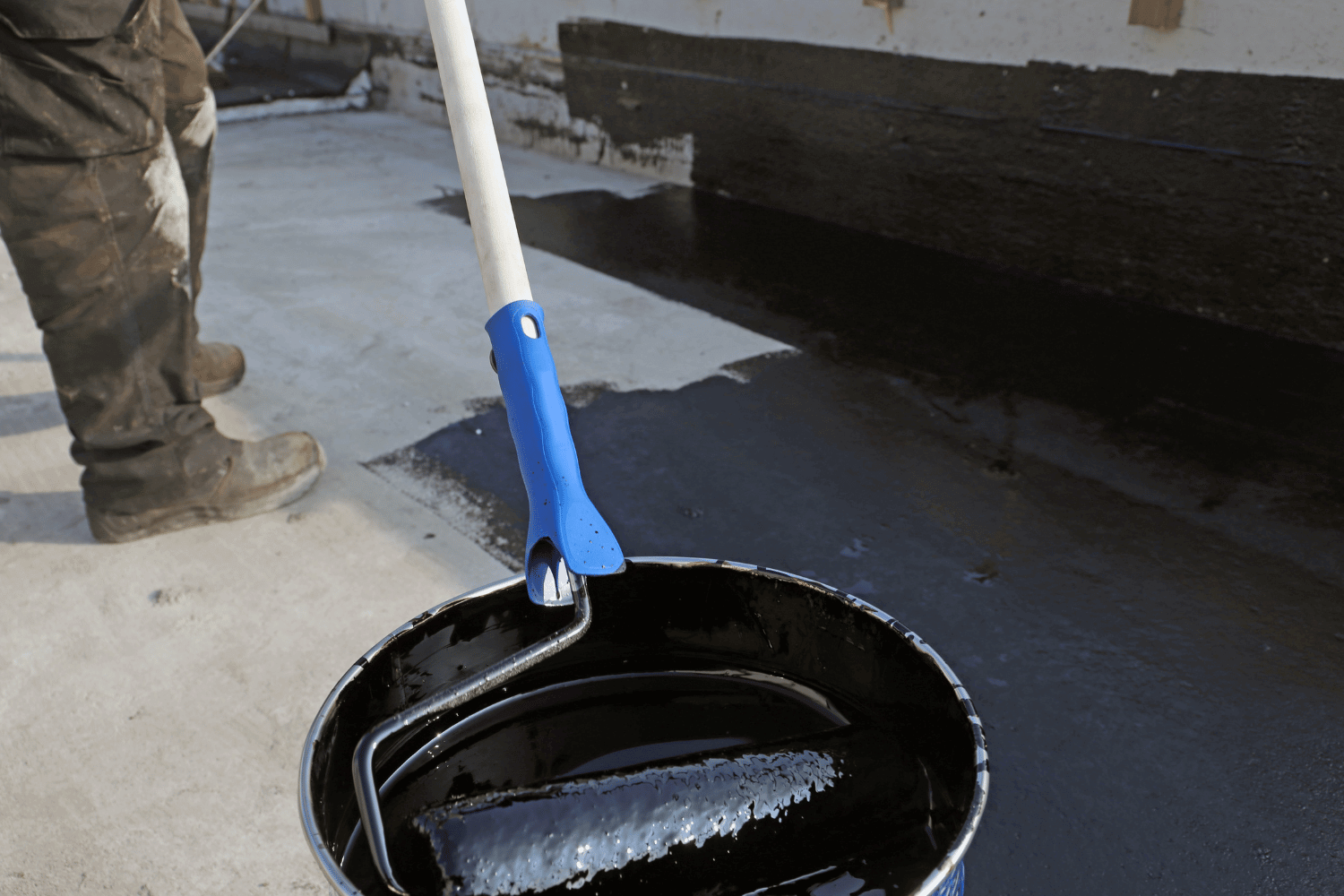
Top-rated flat roof sealants.
Selecting the right sealant is vital for maintaining flat roofs’ integrity and waterproofing. Liquid Rubber Waterproof Sealant is regarded as the best overall due to its thicker consistency, ideal for larger gaps and cracks. These sealants offer strong waterproofing, extending flat roofs’ lifespans by preventing leaks.
Proper surface preparation and application techniques are vital for these sealants’ effectiveness. This section will introduce top-rated sealants, including liquid rubber, elastomeric, and silicone sealants, each offering unique benefits for flat roofing applications.
Liquid Rubber Sealants
Liquid rubber sealants like Rubberseal offer superior water protection and durable membranes, effectively withstanding pooling water and temperature changes. Flex Seal Liquid forms a strong waterproof barrier that withstands extreme weather, demonstrating robust durability.
The elastomeric properties of liquid rubber sealants allow them to expand and contract, preventing cracks and ensuring long-lasting performance. This flexibility and UV resistance make them a practical choice for various roofing applications, providing reliable protection against water damage and environmental challenges.
Elastomeric Sealants
Elastomeric sealants are known for flexibility and stretchability, offering excellent adhesion and accommodating roofing material movement. Often available in white, these sealants enhance reflectivity and energy efficiency, making them a cost-effective flat roof solution.
Their capacity to expand and contract with temperature changes ensures a durable, watertight seal, preventing leaks and extending the roof’s lifespan. Elastomeric sealants are a versatile and effective option for maintaining the integrity of flat roofing systems.
Silicone Sealants
Silicone sealants are prized for their exceptional waterproof properties, suitable for various weather conditions. UV rays resistance and uv resistant properties help maintain their integrity under sunlight, ensuring long-lasting performance.
Silicone sealants form a long-lasting barrier, enhancing roof waterproofing durability. Superior protection against water infiltration and environmental elements makes them reliable for residential and commercial flat roofs.
Professional Help for Flat Roof Waterproofing
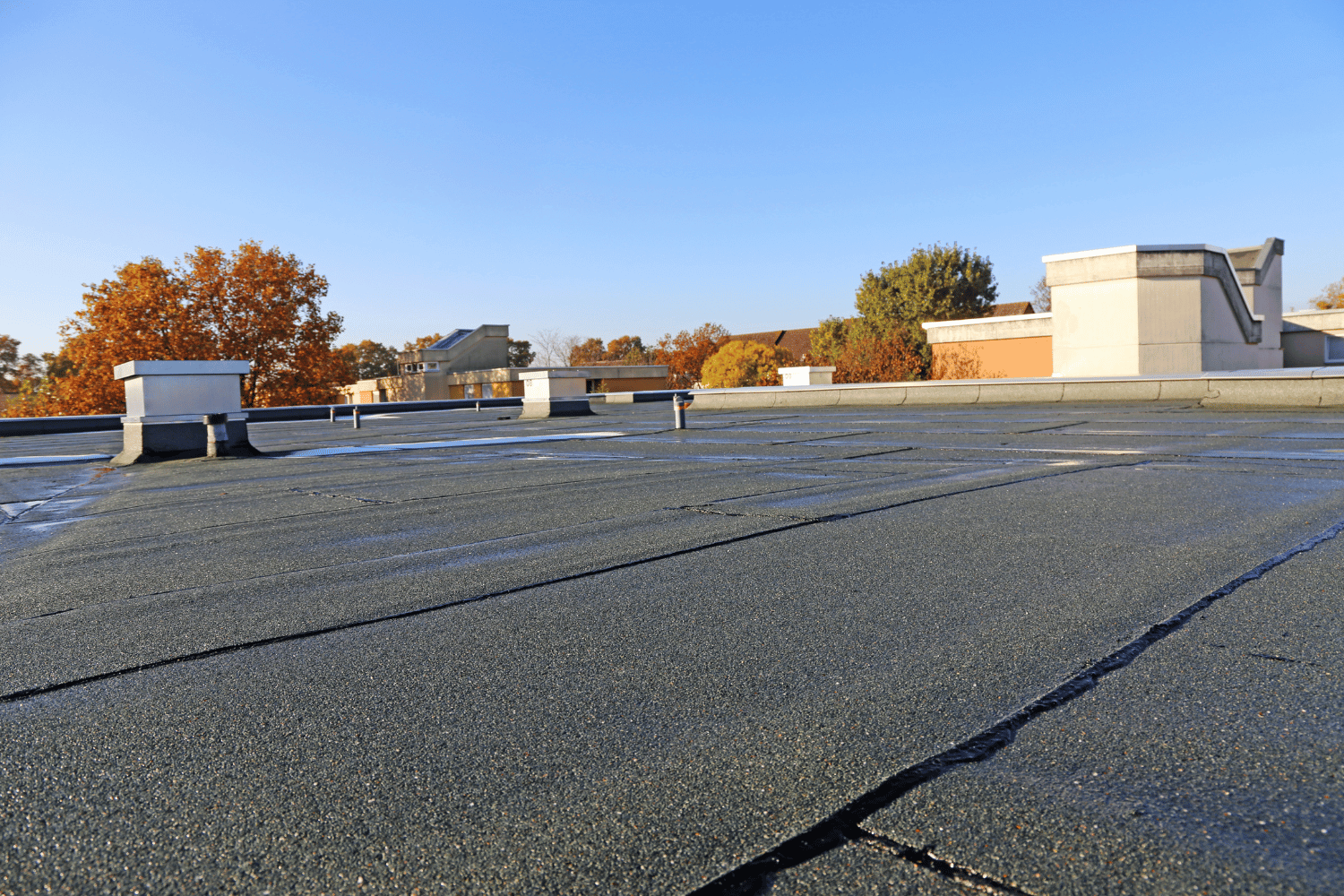
Professional help for flat roof waterproofing.
Hiring professionals for flat roof sealant application is vital due to the task’s time-consuming nature and specific skills required. CoMo Premium Exteriors provides services including emergency repairs, routine maintenance, residential roofing, and commercial roofing repair. Their use of top-grade roofing materials ensures durability and high-quality roof replacement results.
Regular professional inspections can catch hidden issues that may cause significant damage, maintaining the roof’s condition. CoMo Premium Exteriors assists with insurance claims for hail or storm damage, leveraging extensive experience to simplify the process. Customers highly rate CoMo Premium Exteriors for superior customer service, quick response times, and quality workmanship.
CoMo Premium Exteriors is committed to the community through local project involvement, enhancing aesthetic and structural resilience. They offer warranties including a 5-Year Workmanship Warranty and a 1-Year Clean Up Guarantee, providing peace of mind and quality assurance.
Summary
Waterproofing a flat roof is essential for protecting the structure and extending its lifespan. Regular inspections, proper maintenance, and choosing the right waterproofing methods and sealants can prevent water damage and costly repairs. By understanding the unique challenges of flat roofing and taking proactive measures, homeowners and commercial property managers can ensure their roofs remain in top condition.
Whether you opt for DIY solutions or professional help, the key is to act promptly and effectively. CoMo Premium Exteriors is here to assist with all your flat roofing needs, offering expert services and quality materials to keep your roof waterproofed and durable. Trust in the expertise and commitment of professionals to safeguard your investment and maintain the integrity of your flat roof.
Frequently Asked Questions
Which coating is best for a flat roof?
The Ure-A-Sil (urethane-silicone) System is considered the best flat roof coating due to its superior performance and value, while silicone-based coatings like ROOF X TENDER 985 are ideal for roofs prone to ponding. Choosing either option will ensure optimal protection for your flat roof.
Why is waterproofing essential for flat roofs?
Waterproofing is essential for flat roofs as it prevents water damage and extends the roof’s lifespan. Given their vulnerability to water pooling, effective waterproofing safeguards the building’s integrity and prevents costly repairs.
What are the common signs of damage to look for during a flat roof inspection?
During a flat roof inspection, common signs of damage include blisters, cracks, alligatoring patterns, and standing water that remains for over 48 hours, indicating potential drainage problems. Address these issues promptly to maintain the roof’s integrity.
What are the benefits of using liquid waterproofing solutions for flat roofs?
Using liquid waterproofing solutions for flat roofs provides excellent UV resistance and creates a seamless, flexible membrane that prevents water infiltration. This makes them a highly effective option for protecting your roof from potential water damage.
How do reinforced bitumen membranes (RBM) ensure the durability of flat roofs?
Reinforced Bitumen Membranes (RBM) ensure flat roof durability through their multi-layer applications and strong materials, which offer excellent waterproofing, puncture resistance, and UV resistance. This makes RBMs an outstanding choice for maintaining long-lasting roof protection.